Eco-Friendly and Creatively Inspired: The Maas Brothers Automated Powder Coating Line
Maas Brothers Powder Coating has long been RoHS compliant and committed to eco-friendliness.
Eco-Friendly and RoHS Compliant
As a California manufacturer, we recognize the importance of conserving water — and have for a long time. One of the important things we decided when we first invested in our automated line was to spend up to save water.
Take a tour of our facility and you’ll see our 5-stage closed loop wash and pretreatment (no drain) system in action:
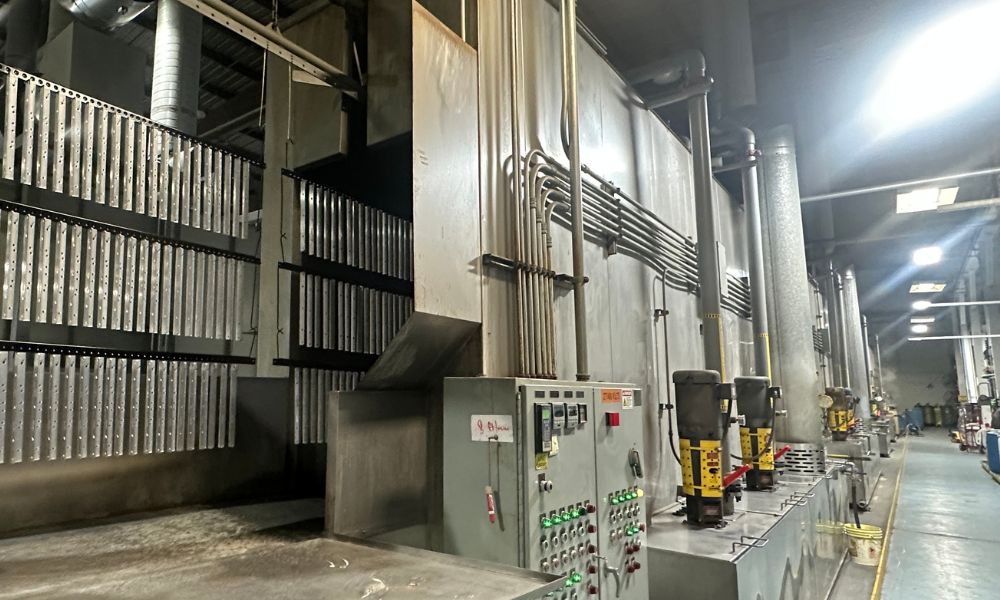
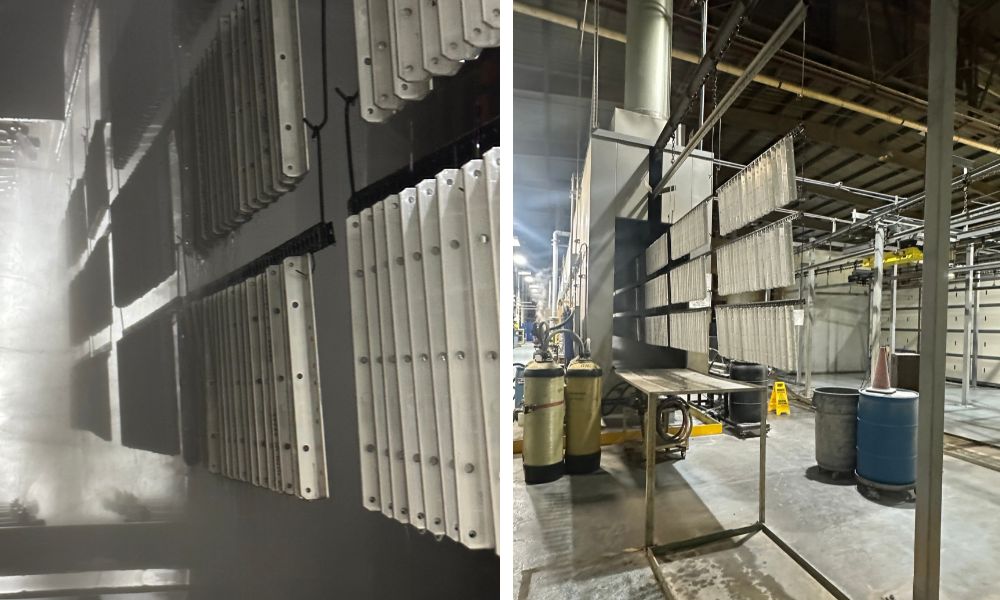
- Our pretreatment process starts with a phosphate cleaner stage, then moves through three water rinse stages.
- Water is not commingled: after the first four stages. Instead, the water goes through an RO system and is filtered back into the system.
- The final (fifth) stage is a nano-particle non-chromate sealer that dries in place and needs no rinsing.
Sustainably engineered, the Maas Brothers 5-stage wash and pretreatment system only uses one gallon of water per minute — and that’s all from evaporation. Companies with systems lacking this technology can waste as much as five gallons a minute – all right down their drain.
Sustainably Smart Investing Helps Customers, too
Delivering excellent results for customers while making strategic investments and conserving resources has been part of the company’s DNA since brothers Kevin and Kraig Maas first founded their company over 25 years ago.
Case in point: when we invest in new powder coating technology, we don’t immediately trash or retire the original equipment. Instead, we brainstorm ways to repurpose our original equipment and reengineer it to better serve our clients.
A great example of this is the most recent expansion of our automated conveyor line.
Improving Our Processes by Integrating New Powder Coating Capabilities with Legacy Ones
Not too long ago, Maas Brothers added a state-of-the-art quick color change booth to our automated powder coating line. It includes both automated powder guns and augmenting manual gun options, as well as integrated powder reclaim capabilities.
This streamlined technology gave us the flexibility to offer our highly efficient and RoHS compliant automated powder coating services to more customers representing more industries than historically possible – regardless of run size or job complexity. It helps that our conveyorized powder coating system has always accommodated parts up to 12 1/2 feet in length!
But we went even further with our capital equipment investment strategy. Instead of decommissioning our original automated powder coating booths and our two legacy manual powder coating booths, we reconsidered their use on the conveyor line.
Strategic Powder Coating Investments That Benefit Our Customers and Their Products
At Maas Brothers, our vision is always to do more work in less time with minimal waste – all without compromising coating quality. In this case, we wanted to offer better powder color flexibility to our customers and improve coating options, too.
To help us get there, as we installed the new quick color change booth, we also expanded the system’s footprint and reconfigured the line by enhancing some of our existing equipment and investing in others.
These additional enhancements included:
- Installing tracks on the shop floor so that our legacy automated powder coating booths are easily pushed quickly on and off the line as needed.
- Upgrading our legacy manual booths to add automated powder coating capabilities so we could offer in-line automated priming and other second coat needs on the line.
- Investing in two new infrared (IR) ovens and strategically placing them on the line to facilitate pre-gelling between coats while also reducing cross-contamination risk.
The result: A custom-engineered, state-of-the-art conveyorized powder coating system that is arguably now the most agile in all of Northern California.
Projects of different run sizes, varied colors, different part complexities – even multiple-coat finishing needs… Maas Brothers now caters to virtually every customer’s unique requirements, all while achieving consistent results without compromise.
Engineering Eco-Friendly and More Sustainable Industrial Powder Coating Services
Prior to our system’s new configuration, we were limited in what automated powder coating services we could offer customers. Changing colors meant stopping production for several hours just to clean the booths and avoid cross-contamination issues. To compensate, we had to handle more jobs with batch powder coating, which takes more time and is inherently less efficient than automated powder coating services.
Now, since installing our quick color change booth, we can change a color in 10 minutes. This helps us achieve optimal throughput without limiting customer options – and without stopping the production line. For our customers, that means greater access to the efficiencies of automated powder coating with much greater color flexibility – even when we are working with prototypes or super-short runs.
More Color Options, Less Time to Market
Maas Brothers’ enhanced flexibility helps our customers offer their end users more design options while reducing their overall costs and go-to-market time.
- Our legacy automated powder coating booths remain the effective workhorse they have always been – we just don’t use them all the time. Instead, we have dedicated these original booths to powder coat parts with our most popular shade of white.
- As those jobs come through, we push our legacy booths onto the line, already prepped and ready to go. Then, when those runs are finished, we push the booths off the line to clean them.
- Meanwhile, the conveyor never stops because products down the line are being powdered using the quick color change booth.
Reduced Downtime and Increased Throughput – Even for 2-Coat Needs
Upgrading our legacy manual booths to add automated powder coating capabilities has been a game changer for some of our customers, and for us. It allows us to handle 2-coat powder coating needs with a single turn of along our conveyor system, saving time, materials, energy, manpower, and water in the bargain.
This is true whether parts need priming or require extra thickness, which is particularly important for some functional coatings (including EV battery coatings). And it’s true even for prototypes or small runs of different colors.
All of this innovation and investment makes our operations run more smoothly, more efficiently, and more sustainably. That’s good news for our environmental impact — and for our customers, too!
Want to see our innovative conveyor system in action? Reach out and schedule a tour of Maas Brothers Powder Coating.